The hazards of choosing inferior vacuum pump intake filters
In industrial production, vacuum pumps are the core equipment for many process flows. However, many users often opt for low-quality vacuum pump inlet filters to save costs, unaware that this practice can lead to serious consequences. This article will delve into the hazards of inferior inlet filters and guide you on how to choose a high-quality vacuum pump inlet filter.
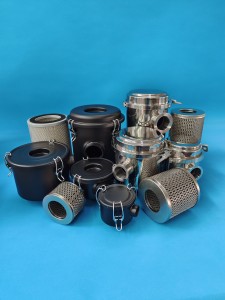
Five Hazards of Low-Quality Vacuum Pump Inlet Filters
- Particles Entering the Pump Cause Wear
Low-quality filters cannot effectively block tiny particles. These hard particles enter the pump chamber with the airflow, rubbing against high-speed rotating vanes or rotors, leading to premature wear of critical components. Long-term use can reduce pump efficiency by over 30% and shorten its lifespan by 50%. - Oil Contamination Accelerates Lubricant Degradation
For oil-sealed vacuum pumps, inferior filters fail to effectively block oil mist and moisture in the air. These contaminants mix with the lubricating oil, causing changes in viscosity, increased acidity, and a significant decline in lubrication performance. - Increased Risk of Chemical Corrosion
Industrial environments often contain acidic gases or corrosive particles. Low-quality filter materials cannot provide adequate protection, allowing these substances to corrode the pump's internal metal components, particularly aluminum alloy parts. - Higher Energy Consumption and Operating Costs
When the filter's resistance is too high or its efficiency is insufficient, the vacuum pump must consume more energy to maintain the required vacuum level. Data shows that using inferior filters can increase energy consumption by 15-25%. - Product Contamination Risks
In clean industries such as semiconductors and pharmaceuticals, poor-quality filters can become sources of contamination, reducing product yield and even causing entire batches to be scrapped.
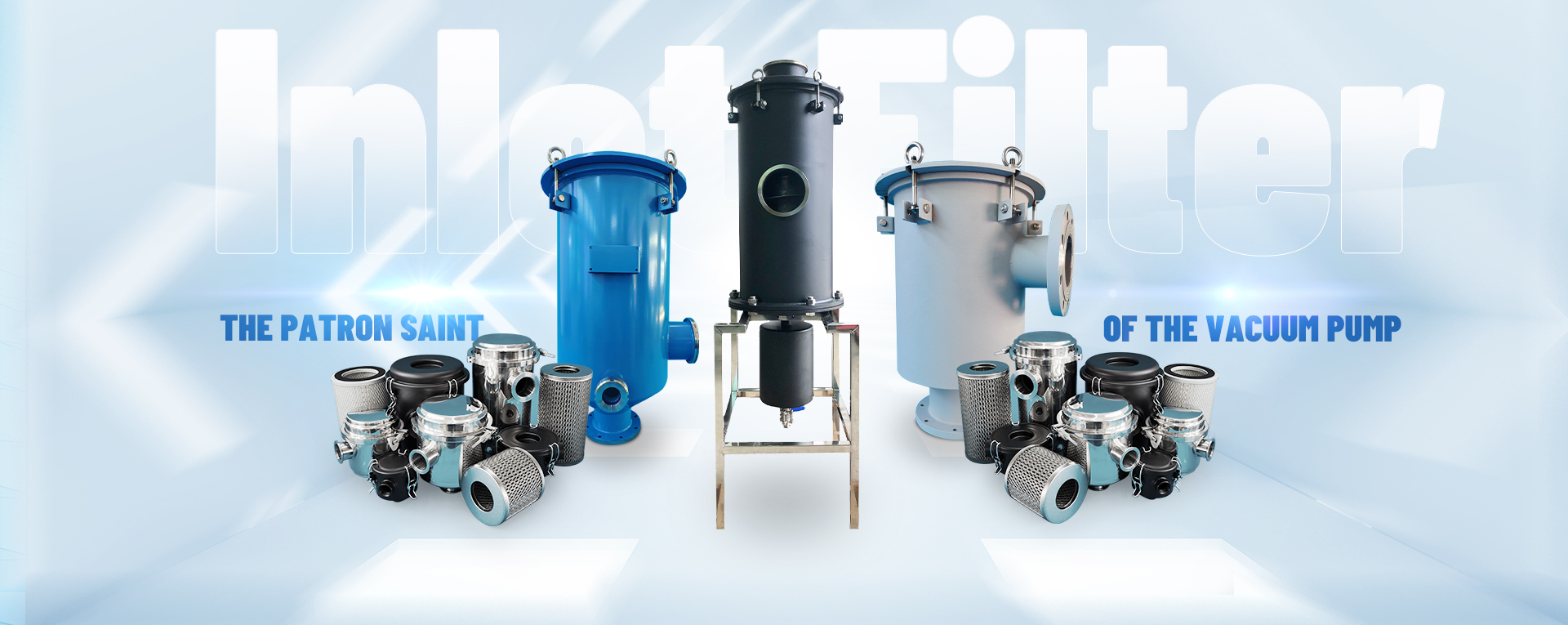
Professional Maintenance Recommendations
- Regular Replacement: Generally, replace every 2,000 operating hours or 6 months; shorten the cycle in harsh environments.
- Pressure Differential Monitoring: Install a differential pressure gauge and replace immediately when exceeding the manufacturer's recommended value.
- Proper Installation: Ensure O-rings are intact, install in the correct direction (follow arrow indicators), and avoid bypass leakage.
- Storage Conditions: Store spare filters in a dry, clean environment away from direct sunlight.
Although the vacuum pump inlet filter is a small component, it plays a crucial role in the overall health of the vacuum system. Choosing a high-quality filter may seem like a higher initial cost, but it significantly reduces equipment maintenance expenses, minimizes downtime losses, and extends the vacuum pump's service life.
Smart users don’t cut corners on filters to save small amounts of money while taking on huge risks. Instead, they see it as a critical investment in ensuring production continuity and product quality.
Remember: A high-quality vacuum pump inlet filter is the first line of defense for protecting your vacuum system—and the most cost-effective insurance measure!
Post time: Apr-09-2025